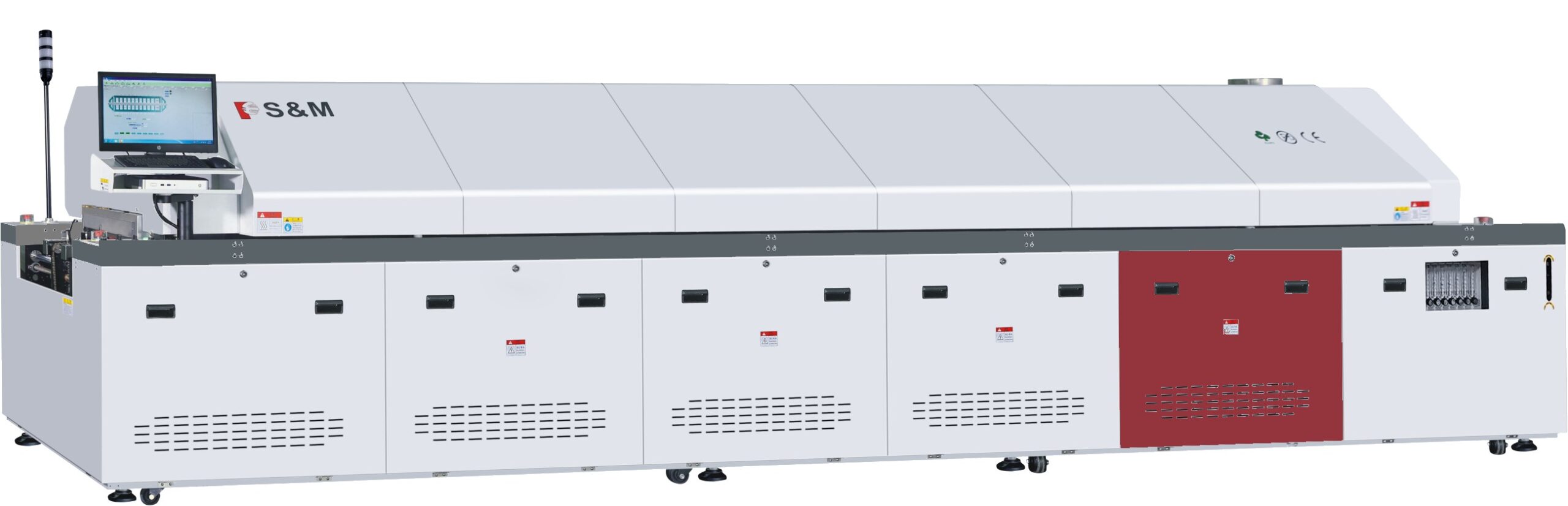
Equipment’s Main Features
- Precise Temperature Control: Multi-point monitoring temperature control system, real-time monitoring of temperature fluctuations, PID automatic adjustment, temperature control accuracy of ±1°C.
- Void Rate: Under a vacuum environment, the void rate inside the solder joint is greatly reduced to ≤3%, which can effectively improve the thermal conductivity and reliability of welding.
- Improve Wettability: The vacuum environment helps to improve the wettability of solder paste to pads and electronic components, allowing the solder to fully contact the pads and enhance welding strength.
- Reduce Oxidation: The oxidation phenomenon during the welding process is effectively suppressed, which helps to reduce the oxide layer on the surface of the solder joint and improve the electrical performance and reliability of the solder joint.
- Wide Range of Applications: Widely used in the manufacture of high-reliability products such as aviation, aerospace, military industry, semiconductor packaging, high-density interconnection boards, automotive electronics, 5G equipment, etc.
- Excellent Quality: using high-quality components, combined with years of development experience and customer feedback, continuous improvement, and optimization.
Detailed Display-Aluminum Alloy Vacuum Chamber
The vacuum chamber is precisely made from aluminum alloy. This aluminum alloy vacuum chamber balances lightweight design, efficient thermal management, and process reliability in reflow soldering. Its density is only one-third that of stainless steel, greatly reducing equipment weight and easing movement or integration into automated production lines. Additionally, the thermal conductivity of aluminum alloy is much higher than that of stainless steel, allowing it to quickly transfer heat during welding and minimize damage to PCBs or components caused by localized overheating.
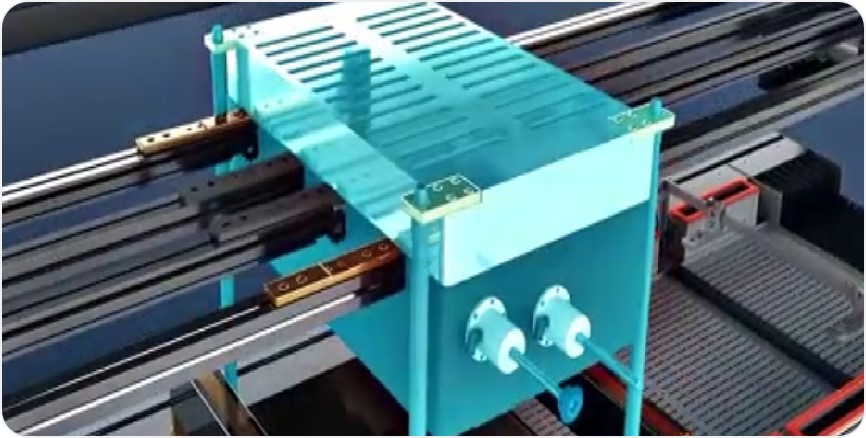
Detailed Display – Heating Furnace Structure
The furnace uses a new type of thermal insulation structure, optimizing the separation of the inside and outside of the furnace, leaving a gap in the middle, and connecting with multiple connection points to ensure strength. At the same time, the insulation layer is thickened and uses a new type of environmentally friendly material that does not cause stinging: aluminum silicate fiber cotton, which effectively blocks the high temperature in the furnace from being conducted outward, greatly reducing heat leakage, and reducing the surface temperature of the equipment and energy consumption.
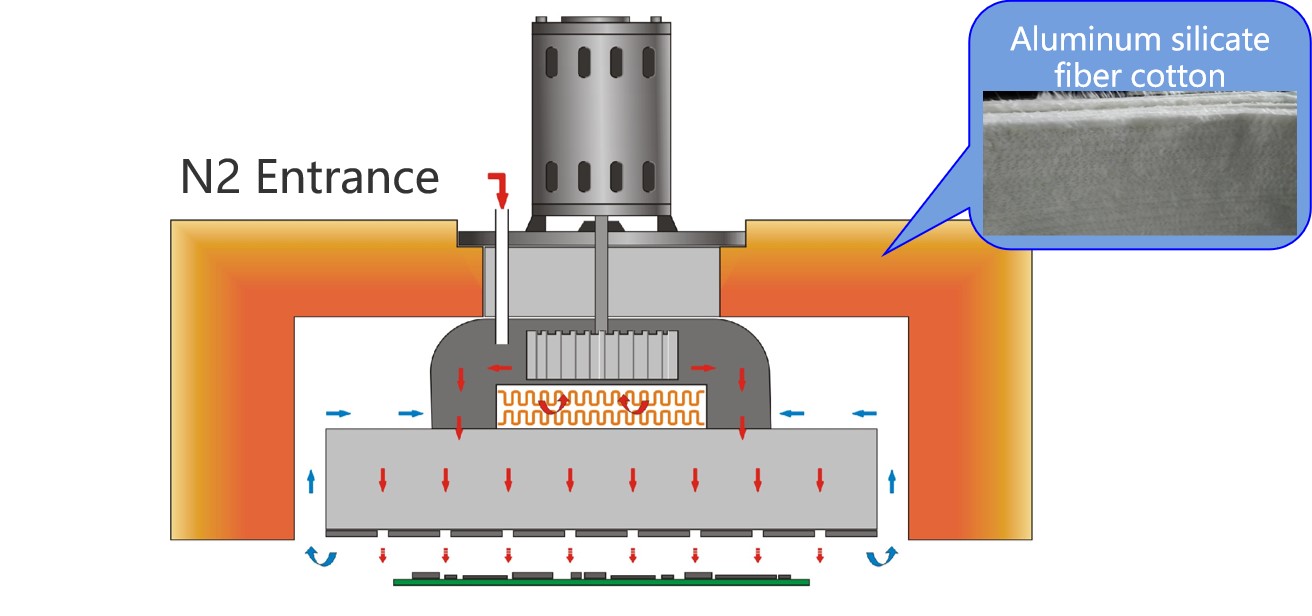
Comparison of Welding Void Ratio
The application of a vacuum environment in the solder melting stage is a very effective and proven key process technology to improve the quality of high-reliability electronic assembly welding (especially reducing the void rate). After product test comparison, compared with traditional atmospheric pressure reflow soldering, the bubble escape rate is increased by 5-8 times; the void rate of solder joints is ≤3%.
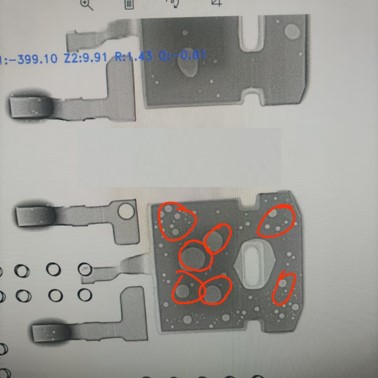
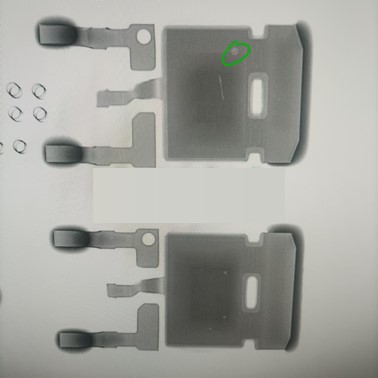
Air furnace/Nitrogen furnace Vacuum furnace
Use Cases
1. Significantly reduce the void rate of solder joints: When soldering is carried out in a vacuum environment, the void rate of solder joints can be stably controlled at ≤3%. This indicator is significantly better than the traditional normal pressure process, greatly improving the density and long-term reliability of solder joints. 2. Effectively inhibit welding oxidation: The vacuum environment significantly reduces the oxygen partial pressure, inhibiting the oxidation reaction of molten solder and solder joint surface from the source. This not only reduces the formation of the oxide layer, but also directly improves the conductivity, thermal conductivity efficiency and mechanical strength of the solder joint.