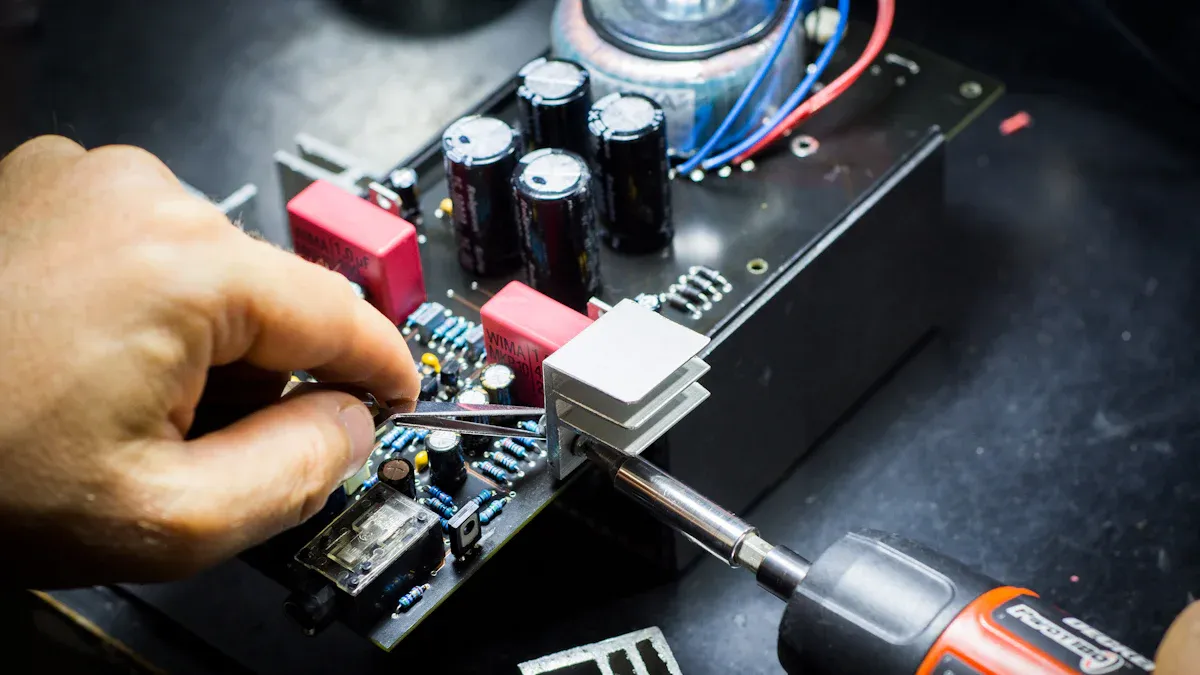
Selecting a Reflow Oven starts with understanding your specific requirements. When selecting a reflow oven, it’s essential to align the oven’s features with your project needs. Key factors to consider include:
-
Precise temperature control for consistent heating
-
The most suitable heating technology for your type of circuit board
-
Size constraints and budget considerations
-
Production volume and desired solder joint quality
-
Compatibility with lead-free soldering processes
-
Reliable brands and strong after-sales support
For instance, selecting a reflow oven with heat settings that match your solder paste can prevent common issues. Brands like chuxin offer a variety of options tailored to different needs.
Key Takeaways
-
Pick a reflow oven that matches your work size, board size, and budget. This helps you get the best results.
-
More heating zones and good temperature control help make strong solder joints. They also help stop problems from happening.
-
Using nitrogen in your oven can lower oxidation. It can make solder better and use less heat.
-
Choose the right oven type for your job. Use a benchtop oven for small jobs. Use a batch oven for medium jobs. Use a conveyor oven for big jobs.
-
Take care of your oven and check it often. This keeps it working well and saves money on repairs.
Selecting a Reflow Oven
Assess Production Needs
When you pick a Reflow Oven, first know what you need. Look at where you will use the oven. Think about what products you want to make. Every production line is different, so you need an oven that fits your work.
-
Think about how many boards you need to make each day and what kinds of products you have.
-
Check if your boards are hard to heat. Some have big parts, and some have small, fragile parts.
-
Make sure the oven can reach the right temperature for your process. Some solder pastes need very careful heat control.
-
If you need to make lots of boards fast, you might need a bigger oven or one with a conveyor.
-
Measure your biggest board. The oven must be big enough for it.
-
Decide how many heating zones you want. More zones help you control the heat better.
Tip: Conveyor-type reflow ovens are good for making lots of boards. They help your line run smoothly. Convection ovens heat boards evenly and work well for boards with many parts.
You should also think about how flexible the oven is. If you change what you make a lot, get an oven with settings you can program. This lets you switch jobs fast and keeps your work moving.
Set Budget
How much money you have is important when picking a Reflow Oven. Your budget will decide what size, features, and quality you can get. Ovens with more features, like more heating zones and better heat control, cost more. These features help you make better solder joints and have fewer problems, especially with tricky boards.
Here is a table that shows prices and features for different ovens:
Production Scale |
Product Model |
Price Range (USD) |
Power (W) |
Notes |
---|---|---|---|---|
Medium-scale |
RS220 |
25,800 – 28,600 |
6,000 |
Semi-automatic vacuum reflow oven, welding area 220x220mm |
Small-scale |
QRF320 |
N/A |
4,500 |
Benchtop reflow oven, 5-zone heating system |
Medium-scale |
MD Series |
N/A |
5,000-7,000 |
Medium sized infrared or hot air reflow ovens |
Medium-scale |
IRO850 |
N/A |
N/A |
Inline reflow oven for small to medium series production |
Large-scale |
SUNY-SMT640 |
N/A |
18,000 (starting power) |
High power machine with PLC control |
If you do not have much money, you may need a simple oven with just one heating zone. These are good for small jobs or easy boards. If you can spend more, you can get an oven with more zones. These ovens control heat better, save energy, and have cool features like feedback and moving conveyors.
-
If you have less money, you will get a basic oven, but it can still work well.
-
If you have more money, you can buy an oven with more zones, better energy use, and easier cleaning.
-
Think about after-sales help and warranty. These come with expensive ovens and can save you money later.
Picking a Reflow Oven that fits your needs and budget helps you get the most for your money. Always match your spending to what you need now and what you might need later.
Oven Types
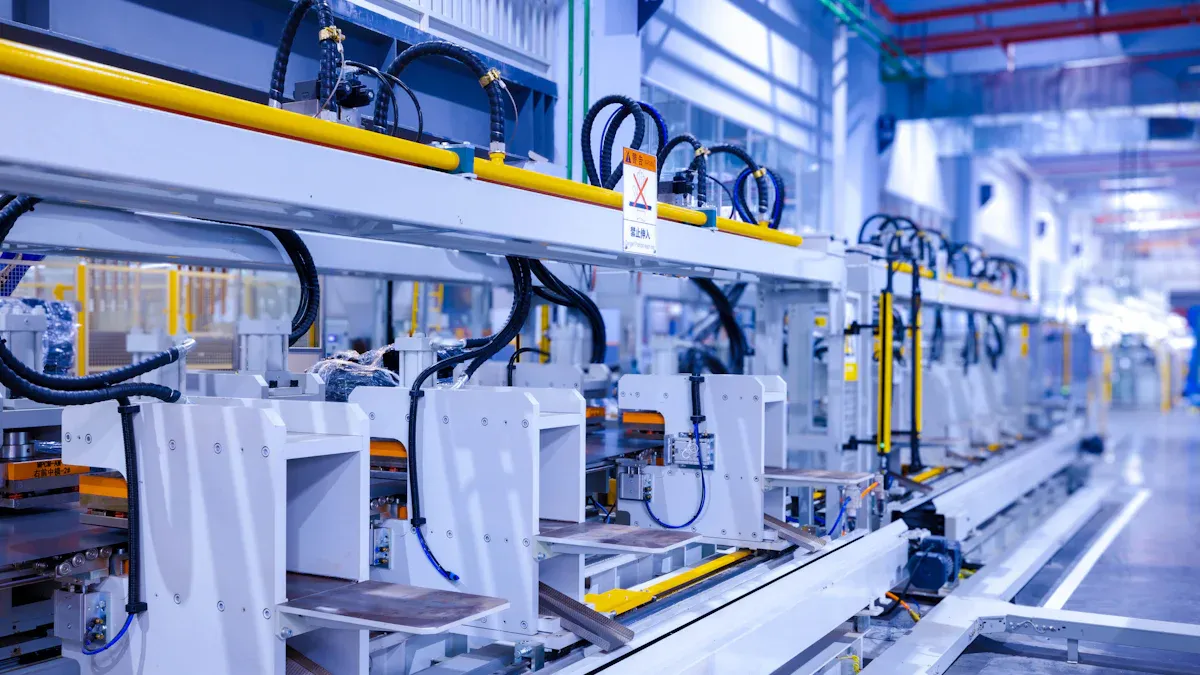
When you choose a reflow oven, you need to know the main types. Each oven type fits different jobs and production needs. The three most common types are benchtop, batch, and conveyor ovens.
Benchtop
Benchtop ovens work best for small jobs, prototypes, or when you want to experiment. You can place them on a table, and they do not take up much space. You often use these ovens for simple boards or when you need to test new designs.
Advantages:
-
Easy to use. You pick a profile, start the oven, and let it run.
-
Good for both small and large parts on a board.
-
Gives better cooling and heating control than a toaster oven.
-
Works well for rework, like replacing a single part.
Disadvantages:
-
Takes longer to finish each board, so not great for many boards.
-
Some parts, like plastic connectors, may melt.
-
Size limits mean you cannot use them for big boards.
-
You may need more skill to get the best results.
Tip: Benchtop ovens help you learn and test ideas without spending much money.
Batch
Batch ovens handle more boards at once than benchtop ovens. You load a group of boards, run the oven, and then unload them. These ovens give you flexibility for low to medium production.
-
You can use them for boards of different sizes.
-
They cost less than conveyor ovens.
-
You need to load and unload boards by hand.
-
The quality depends on how you set up and run the oven.
Batch ovens work well if you want to make several boards at a time but do not need full automation.
Conveyor
Conveyor ovens suit high-volume production. You place boards on a moving belt, and the oven heats them as they travel through. This type gives you steady, repeatable results.
Key benefits:
-
Handles many boards quickly with less labor.
-
Keeps product flow smooth and quality high.
-
Uses features like dual insulation and smart cooling to save energy and cut costs.
-
Advanced systems reduce downtime and make cleaning easy.
Oven Type |
Best For |
Pros |
Cons |
---|---|---|---|
Benchtop |
Prototyping, small jobs |
Simple, flexible, low cost |
Slow, size limits, manual work |
Batch |
Low/medium runs, varied sizes |
Flexible, handles more boards |
Manual loading, operator skill needed |
Conveyor |
High-volume, uniform products |
Fast, automated, consistent quality |
Expensive, less flexible |
You should pick the oven type that matches your production needs, board size, and budget. This choice helps you get the best results for your work.
Heating Zones
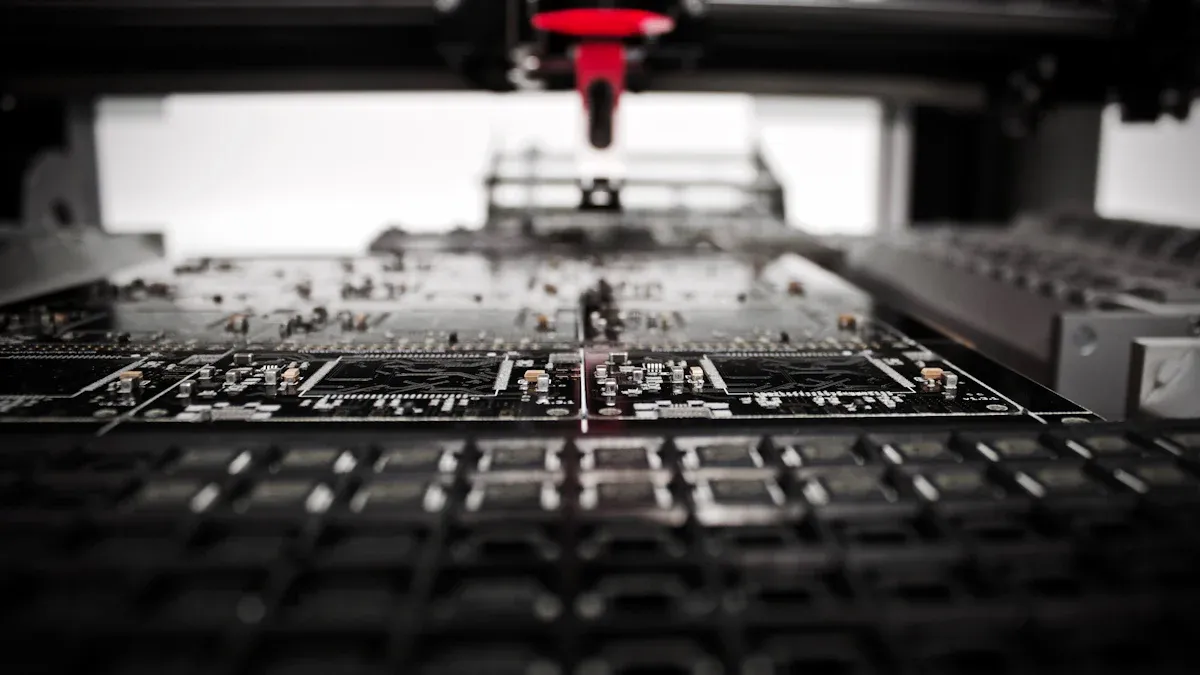
Zone Number
When you look at reflow ovens, you will see that each oven has a certain number of heating zones. Each zone is a separate area inside the oven with its own temperature control. More zones mean you can control the heat more precisely as your circuit board moves through the oven.
If you choose an oven with more heating zones, you get better control over the temperature profile. Each zone uses a special control system to keep the temperature steady. This helps you match the heat to your board and the parts on it. Good control is important because it helps you avoid problems like cold solder joints or burnt components.
More heating zones give you the power to adjust the heat step by step. This makes it easier to get high-quality soldering results, even with complex boards.
You should think about your product and how much control you need. Simple boards may only need a few zones. Complex boards with many parts or special materials often need more zones for the best results.
Zone Configuration
The way you set up the heating zones in your oven is called the zone configuration. Most reflow ovens use four main zones: Preheat, Soak, Reflow, and Cooling. Each zone has a special job:
-
Preheat Zone: Warms up the board and starts the soldering process.
-
Soak Zone: Makes sure the whole board heats evenly, so all parts reach the right temperature.
-
Reflow Zone: Raises the temperature high enough to melt the solder and make strong joints.
-
Cooling Zone: Lowers the temperature slowly to make the solder solid and prevent damage.
If you keep each zone at the right temperature, you get even heating and strong solder joints. Problems like broken heaters or poor airflow can cause uneven heat, which leads to bad soldering. You should check your oven often and use monitoring tools to keep the zones working well.
Zone Name |
Purpose |
---|---|
Preheat |
Activates flux, removes solvents |
Soak |
Evens out temperature across the board |
Reflow |
Melts solder for joint formation |
Cooling |
Solidifies solder, prevents thermal shock |
Tip: Regular maintenance and calibration help you keep your oven zones working at their best. This reduces defects and keeps your boards reliable.
Temperature Control
Precision
You need to control the temperature very carefully in a reflow oven. Even small changes in heat can change your results a lot. For lead-free soldering, pick an oven that keeps the temperature within one degree Celsius. This is important because lead-free solder paste melts at high heat, between 235°C and 245°C. Most electronic parts can only handle up to 250°C or 260°C. That means you do not have much room for mistakes. If the oven gets too hot, your parts might get damaged. If it is not hot enough, the solder will not melt right and your joints can be weak.
Tip: Always check your temperature before you start. One small mistake can ruin all your boards.
A good reflow oven lets you set the exact temperature you need. It keeps the heat steady so you avoid problems. Look for ovens with digital controls and easy-to-read screens. These make it simple to set the right temperature every time.
Uniformity
It is just as important to keep the heat even in the oven. If some spots are hotter or cooler, your boards will not heat the same way. This can cause problems like tombstoning, where small parts stand up, or warping, where the board bends. These issues make your boards less reliable and cost more to fix.
In PCB assembly, you want every board to get the same heat. Good reflow ovens use special fans or airflow to spread heat everywhere. This helps stop defects and gives you the same results each time.
-
Uneven heat can cause:
-
Bad solder joints
-
Bent or twisted boards
-
More mistakes
-
Note: Keeping the temperature steady means better boards and fewer problems.
When you pick a reflow oven, ask about how even the heat is. A good oven keeps the temperature almost the same everywhere inside. This helps you make strong boards and waste less.
Board Transport
Conveyor Systems
You need to think about how your boards move through the reflow oven. Conveyor systems help you move boards from one end of the oven to the other. These systems use belts or rails to carry each board at a steady speed. You can set the speed to match your production needs.
A good conveyor system keeps your boards safe. It stops boards from bumping into each other or falling off. Some ovens use mesh belts, while others use edge rails. Mesh belts support the whole board. Edge rails hold the board by its sides. You should pick the system that fits your board size and shape.
Tip: Mesh belts work well for small or thin boards. Edge rail conveyors help with heavy or large boards.
Here is a quick comparison:
Conveyor Type |
Best For |
Key Benefit |
---|---|---|
Mesh Belt |
Small, light PCBs |
Full board support |
Edge Rail |
Large, heavy PCBs |
No contact with bottom |
Cycle Time
Cycle time means how long it takes for one board to travel through the oven. You want a short cycle time if you need to make many boards fast. Conveyor speed and oven length both affect cycle time.
You can adjust the conveyor speed to match your soldering process. Faster speeds mean more boards per hour. Slower speeds give more time for heating and cooling. You must balance speed with quality. If you go too fast, solder may not melt right. If you go too slow, you waste time and energy.
-
Check your production goals.
-
Set the conveyor speed to meet those goals.
-
Watch for defects if you change the speed.
Note: Always test your process before full production. This helps you find the best cycle time for your boards.
Inert Environment
Nitrogen Use
You can get better soldering by using nitrogen in your reflow oven. Nitrogen pushes out oxygen and small particles from the oven. This makes a safe space that keeps your boards safe during soldering. With nitrogen, your solder joints look cleaner and shinier. The solder spreads better, and you see fewer mistakes. Nitrogen also helps heat move faster and more evenly in the oven. This means your boards heat up quickly and safely, which protects delicate parts and saves power. Workers can see inside the oven better, so they can find and fix problems sooner.
Here is a table that shows how nitrogen helps your solder joints:
Benefit |
Impact on Solder Joint Quality |
---|---|
Reduced Oxidation |
Stops oxide from forming, so solder flows better and joints are stronger, cleaner, and brighter |
Improved Solder Wetting |
Helps solder spread and fill better, making joints stronger and more reliable with fewer mistakes like bridges or gaps |
Lower Oxygen Levels |
Lets you solder at lower heat, which keeps parts safe and saves energy |
Process Stability |
Gives steady soldering, so more boards pass the first time and you fix less |
Reduced Flux Residue |
Cuts sticky leftovers by up to 66%, so boards are cleaner and work better |
Oxidation Prevention
Oxidation can cause lots of trouble when you solder. Oxygen in the air reacts with metal on your boards and parts. This makes a layer called oxide that stops solder from sticking well. You want to stop this because it makes weak joints and more mistakes.
Using nitrogen in your oven helps stop oxidation. You will see fewer mistakes and stronger solder joints. Here are some results from using nitrogen:
-
Mistakes drop a lot, for example, from 82 to 37 per million.
-
More boards pass the first check, going up by 5-7%.
-
Tests show big gains. One part failed 183 times in air but only 3 times with nitrogen.
-
Solder spreads at a lower heat, dropping from 270°C to 205°C, which keeps your parts safe and saves power.
Tip: If you want strong boards with fewer problems, think about using a reflow oven with nitrogen. This small change can really help your production quality.
Energy Efficiency
Power Consumption
It is important to know how much power your reflow oven uses. The amount of power depends on the oven’s size and how many heating zones it has. Bigger ovens with more zones use more electricity. For example, the GT-R8 oven has 8 zones and uses about 28KW when you turn it on. If you use nitrogen, it can go up to 30KW. When running normally, it uses between 9 and 10KW. The table below shows some main details:
Parameter |
Value |
---|---|
Oven Model |
GT-R8 (8 zones) |
Startup Power |
28KW / 30KW (N2 option) |
Normal Power Consumption |
9–10KW |
Number of Heating Zones |
Top 8 / Bottom 8 |
Heating Zone Length |
3110 mm |
Conveyor Width |
50–700 mm (dual: 50–280 mm) |
Power Supply |
3Φ380V/50Hz |
Tip: Ovens with more zones let you control heat better but use more energy. Always look at the power rating before you buy an oven.
Cost Savings
Reflow ovens that use less energy help you save money each year. Electricity costs are a big part of your business spending, especially if you make lots of boards or pay high power prices. If you pick an oven that does not use much energy, your bills will be lower. These ovens also help you make more boards with fewer mistakes, so you do not waste money on fixing problems.
A study found that putting a thermal insulation jacket on a reflow oven cut its yearly energy use by about half. This change made electricity costs drop by 70.1%. The company saved over 263,000 baht in one year. They got their money back in less than two years, so the savings started fast.
Note: Picking an energy-saving oven helps you spend less and is good for the environment. Over time, these savings can really help your business.
Maintenance
Reliability
You want your reflow oven to work well every day. Reliable ovens help you finish jobs on time and avoid costly mistakes. If you take care of your oven, you will see fewer breakdowns and better results.
Here are some ways to keep your oven reliable:
-
Clean the oven after each use. Dust and solder paste can build up inside.
-
Check the fans and heaters often. Make sure they run smoothly.
-
Look for loose wires or broken parts. Fix them right away.
-
Lubricate moving parts if the manual says so.
-
Replace worn-out belts or rails before they break.
Tip: Set a regular schedule for maintenance. Write down each task and check it off when you finish. This habit helps you catch problems early.
A reliable oven saves you money. You will spend less on repairs and waste fewer boards. Your production line will run smoothly, and your team will trust the equipment.
Calibration
Calibration means you set your oven to heat at the right temperature. If your oven is not calibrated, your boards may not solder well. You might see weak joints or damaged parts.
You should calibrate your oven at least once every few months. Some ovens have built-in tools for this job. Others need special thermometers or sensors.
Follow these steps to calibrate your oven:
-
Heat the oven to a set temperature.
-
Place a sensor or test board inside.
-
Check if the oven’s display matches the real temperature.
-
Adjust the settings if needed.
Note: Always use the same type of sensor for each test. This practice gives you accurate results.
Calibration keeps your soldering process safe and steady. You will make strong boards and avoid costly errors. Reliable calibration also helps you meet quality standards in your work.
Practical Considerations
PCB Size
You need to check the size of your printed circuit boards before you choose a reflow oven. Each oven model supports a different maximum PCB width. For example, the 1936 MK7 Reflow Oven System can handle boards up to 55.9 cm (22 inches) wide. This size fits most standard and large PCBs. If your boards are bigger than this, you must look for a special oven. Always measure your largest board and compare it to the oven’s specs. Picking an oven that is too small can stop your production or damage your boards.
Tip: Always leave a little extra space for future board designs. This helps you avoid buying a new oven if your board size grows.
Throughput
Throughput means how many boards you want to process in a set time. You must match your oven’s speed and length to your production needs. The right oven keeps your line moving and your boards safe.
-
First, find your required cycle time and board length. This tells you the belt speed you need.
-
For example, a 45 cm board with a 40-second cycle time needs a belt speed of 1.125 cm/sec.
-
A 5-zone oven with a 180 cm tunnel only gives 0.66 cm/sec, which is too slow.
-
A 7-zone oven with a 250 cm tunnel gives 0.926 cm/sec, still not enough.
-
A 10-zone oven with a 360 cm tunnel gives 1.33 cm/sec, which meets your needs.
-
Longer ovens with more zones let you run boards faster and keep good solder quality.
You should pick an oven that matches your throughput goals. If you need to make more boards, choose a longer oven with more zones.
Space
You must plan for the space your reflow oven will use. Large ovens need more room for both the machine and for safe operation. Measure your workspace before you buy. Think about the oven’s length, width, and height. Leave space for loading and unloading boards. Make sure you can reach all sides for cleaning and maintenance.
Oven Size |
Workspace Needed |
Best For |
---|---|---|
Small/Benchtop |
Minimal |
Prototyping, small runs |
Medium |
Moderate |
Batch production |
Large/Conveyor |
Large |
High-volume lines |
Note: Good planning helps you avoid crowding and keeps your work area safe and efficient.
Comparison Checklist
When you pick a reflow oven, you want it to fit your needs. Use this checklist to help you compare ovens. It will help you choose the best one for your work.
Quick Checklist
-
Make sure the oven size matches how many boards you make each day.
-
Count the heating zones and see how they are set up.
-
Check if the oven keeps the temperature steady and heats evenly.
-
Look at the insulation to save energy and keep heat inside.
-
Think about the price and also the cost to run and fix the oven.
-
Decide if you want a conveyor or if you will load boards by hand.
-
Ask how often you need to clean the oven and how easy it is.
-
See if the oven can use nitrogen to make better solder joints.
-
Make sure your biggest PCB will fit in the oven.
-
If you want to work faster, check for automation features.
-
Look at the warranty and what kind of help you get after buying.
-
Remember to add in training and setup costs.
Good insulation helps the oven use less power and keeps the heat even. This protects your boards and saves you money over time.
Feature Table
Feature |
Why It Matters |
What to Look For |
---|---|---|
Heating Zones |
Controls heat at each stage |
More zones for complex boards |
Temperature Control |
Keeps soldering steady and safe |
Digital controls, tight accuracy |
Insulation Quality |
Reduces heat loss, saves energy |
High-temp materials, no hot/cold spots |
Board Transport |
Moves boards safely and quickly |
Conveyor for high volume, manual for small runs |
Energy Consumption |
Affects your running costs |
Lower kW, good insulation |
Maintenance |
Keeps oven working and reduces downtime |
Easy cleaning, simple part replacement |
PCB Size Support |
Fits your largest board |
Check max width and length |
Nitrogen Capability |
Improves solder joints, reduces oxidation |
Option for nitrogen atmosphere |
Automation |
Speeds up production, reduces errors |
Programmable settings, auto conveyors |
Warranty & Support |
Protects your investment |
Long warranty, fast service |
Use this table to compare ovens side by side. Mark which features are most important for your job. This helps you pick the oven that gives you the best value and works well for you.
Brand and Support
Trusted Brands
When you look for a reflow oven, you want a brand you can trust. Trusted brands have a strong history of making reliable machines and helping customers. For example, chuxin offers a wide range of reflow ovens for different needs. You can visit their website at https://www.chuxin-smt.com to see their products and support options.
Many top brands provide more than just the oven. They give you training, fast spare parts, and help when you need it. This support keeps your production running smoothly. Here is a table that shows what some leading brands offer:
Manufacturer |
Support Features |
Global Reach |
---|---|---|
Rehm Thermal Systems |
Training, fast parts, online help |
Europe, Asia |
Heller Industries |
24/7 support, manuals, remote service |
North America, Asia |
BTU International |
On-site setup, spare parts, tech advice |
Global |
Kurtz Ersa |
Training, hotline, local service teams |
Europe, Asia |
I.C.T |
On-site setup, 24/7 support, local service teams, Training |
Global |
You should choose a brand that gives you easy access to help and parts. This choice helps you avoid long delays if something goes wrong.
Service and Warranty
Good service and a strong warranty are important when selecting a reflow oven. Brands with quick customer support and available spare parts help you fix problems fast. You want to keep your line running and avoid losing time.
Look for these features when you compare brands:
-
Clear warranty terms that protect you from unexpected costs
-
Fast technical help, both online and in person
-
Training for your team so they can use the oven safely
-
Easy access to spare parts
A good warranty and strong support give you peace of mind. You know you can get help if you need it.
When you pick a brand, think about how they handle repairs and questions. Brands like chuxin and other top names focus on customer care. They help you keep your oven working well for years. This support makes your investment safer and your production more reliable.
Picking a Reflow Oven is easier if you know what you need. Look for features that fit your type of work and how hard your boards are to make. Some important things to remember are:
-
Use good temperature control and more heating zones for even heating.
-
Pick vacuum reflow or nitrogen if you want strong and clean solder joints.
-
Choose a steady conveyor system and an oven that saves energy for better results.
Look at the comparison table before you choose. Brands like chuxin can help you get the right oven. Start looking with confidence so you can make good boards every time.
FAQ
What is the main difference between a benchtop and a conveyor reflow oven?
A benchtop oven is good for small jobs or testing new ideas. You put each board in by hand. A conveyor oven moves boards on its own. It is used when you need to make lots of boards. Conveyor ovens help you work faster and get the same results every time.
How often should you calibrate your reflow oven?
You should check and adjust your oven every few months. Doing this keeps the temperature right. This helps stop bad solder joints and keeps your boards safe.
Can you use lead-free solder in any reflow oven?
Some ovens cannot use lead-free solder. You need an oven that gets hotter for lead-free solder. Always check the highest temperature your oven can reach. Lead-free solder needs more heat than regular solder.
Why is nitrogen important in reflow soldering?
Nitrogen makes a safe space inside the oven. It stops oxidation and helps solder move better. Your solder joints look cleaner and are stronger. Nitrogen also helps lower mistakes.
What should you do if your boards come out with cold solder joints?
-
Check if your oven is set to the right temperature.
-
Make sure all heating zones are working.
-
Slow down the conveyor if you need to.
-
Use a thermal profiler to check the heat.
Fixing these things will help your solder joints get better.